
Dust Control Systems Ltd has commissioned one of its latest energy saving extraction plants to deal with dust at the Soper Group’s joinery workshops in Hull.
A family-owned and operated concern, based in the centre of Kingston-upon-Hull, The Soper Group Ltd is quite a success story. Roger Soper established Soper Building Services in 1973 as a general building company and within a few years it had expanded to include the manufacture of high quality bespoke joinery. Today, the Group comprises three distinct operations, with each of Roger’s three sons fully involved in key management roles; Mike Soper is production director for joinery manufacture and joinery products, Neil is responsible for construction and building maintenance contracting, and Richard heads up the building plastics stockholding which supplies soffits, fascias and rainwater systems.
A commitment to high quality bespoke joinery manufacture, and a drive to always satisfy their customers’ needs with quality service has earned Soper’s an enviable reputation throughout Yorkshire and beyond. A large proportion of projects undertaken by the company are for local authorities and regional building companies, involving all kinds of standard and bespoke joinery manufacture. Their service also includes the design and manufacture of staircases and traditional box sash windows and facilities include in-house wood finishing.
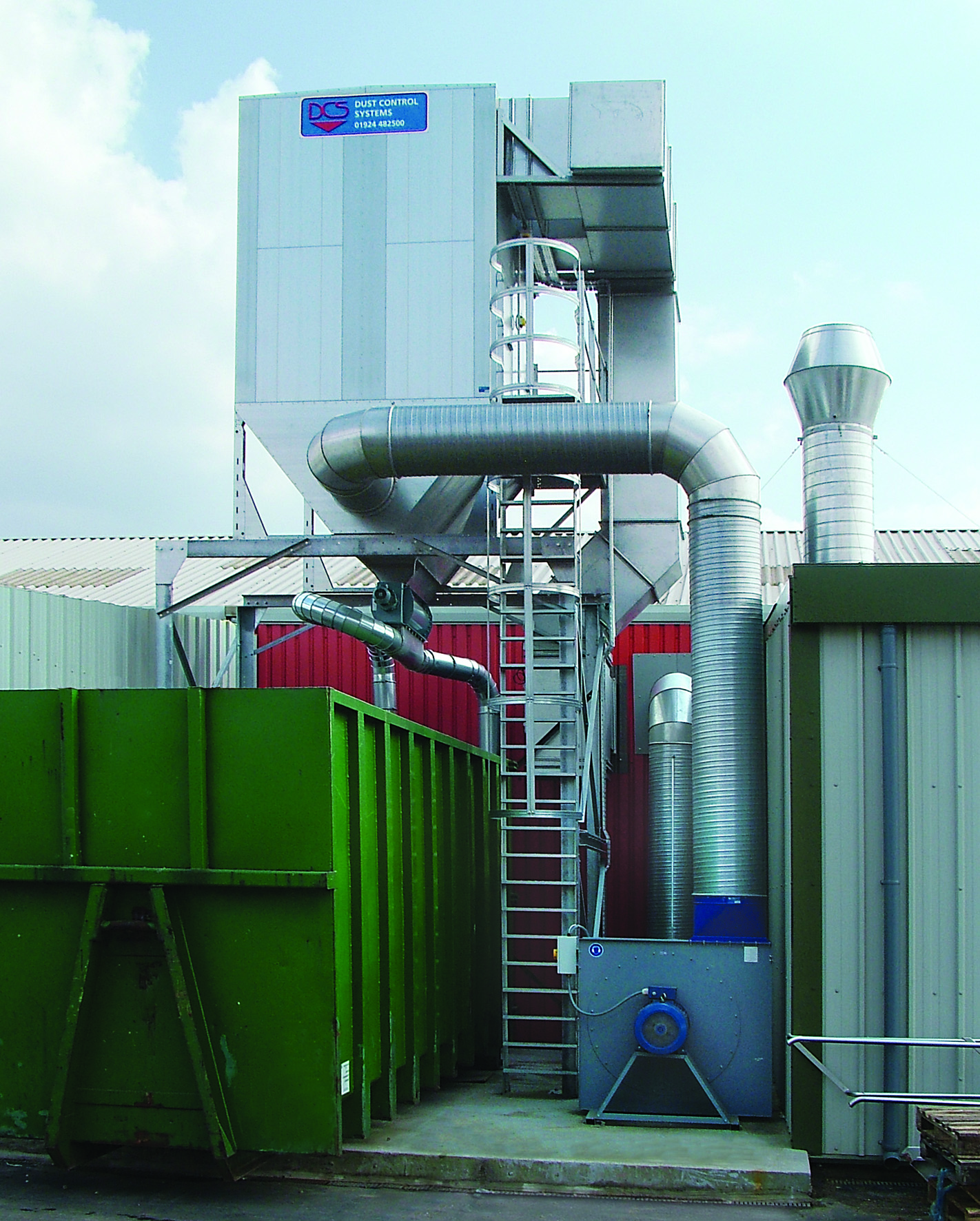
Growth is continuous, and the need to further expand has recently seen the business relocate to larger modern premises with a total floor space of 24,000 sq. ft. The new joinery workshop boasts a list of 34 woodworking machines, all of which required effective dust extraction. Mike Soper explains: “Our previous dust plant was an excessive energy consumer and the concept of bringing our bills down by installing a more energy efficient plant certainly interested us. DCS were able to demonstrate the sort of savings we could expect by installing modern extraction with their Dynamic Drive System; giving us the extraction volumes we need, while cutting energy use. It was an easy decision to make and we are now seeing a considerable drop in electricity bills.”
Melvyn Bathgate, sales director of DCS Ltd, says: “Energy efficiency starts at the initial design stage, with the selection of filter, fans and ductwork to best suit each project. Additionally, at DCS we have successfully introduced variable speed control to our dust extraction systems. Combined with automatically operated dampers, power to the extraction system responds dynamically to meet demand, providing optimum efficiency.”
Dust Control Systems installed an externally located, high-efficiency modular filter system designed to handle an airflow capacity of 17,200m³/hr, although the total airflow of all machines was more than 40,000m³/hr. Selected machines are fitted with pneumatically operated dampers which automatically vary the system’s volume as they open and close. Collected waste is discharged ‘pressure-free’, via a rotary valve, into a storage bunker sited beneath the filter.