Spray booth and drying systems specialist, Gallito Limited, now a brand of Filtermist Systems Limited, has recently completed the installation of a new paint spraying facility for leading furniture manufacturer Ellis Furniture. At its factory in Huddersfield, West Yorkshire, Ellis Furniture design and manufacture strong, durable and safe furniture to meet challenging environments such as schools & universities, care homes and hotels, as well as manufacturing high quality kitchen and bathroom furniture for the retail market.
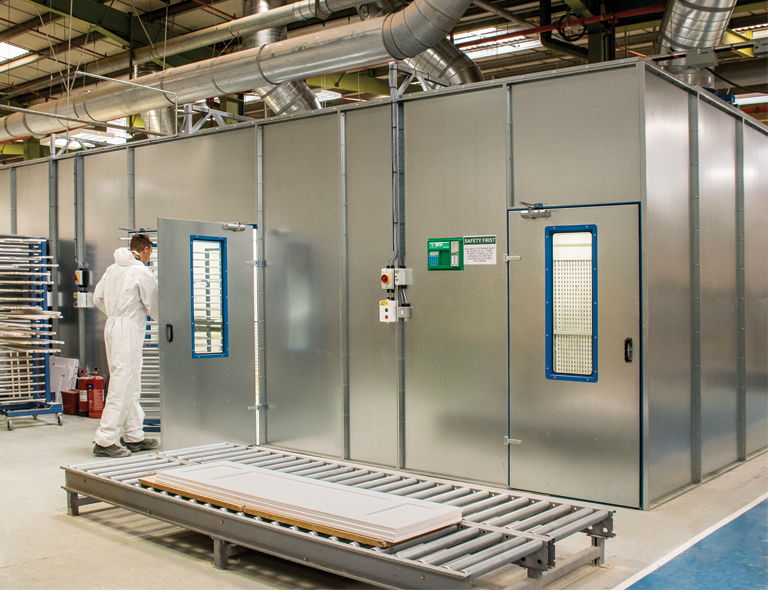
Founded in 1891 by J Thomas Ellis, and at the forefront of UK furniture making for 125 years, Ellis Furniture still remains a privately owned family business. Today, operating from a modern factory with 200,000 sq. ft. of production space, the company designs and manufactures furniture to exacting standards, and utilises a combination of traditional skills with some of the most up to date production machinery of its kind. Manufacturing is complemented by an extensive finishing and assembly facility where the company’s latest investment in technology has been undertaken to fulfil the needs of a changing market requirement.
Ellis Furniture’s engineering manager, Paul Dudley, explains: “Our production processes cover a wide range of materials including high pressure laminates, MFC, real woods and veneers, as well as painting and lacquering a variety of different substrates.
Since the launch of our ‘1891’ painted collection of kitchens and bathrooms, demand for paint-finished products has continued to grow, and the decision was made to invest in an automatic panel spray painting line to manage this increasing demand. However, we needed to retain our capability of undertaking short run and tailored production and, since this would be uneconomic to run on the automatic paint line, we still had a requirement for hand-spraying and a traditional spray booth.”
The company previously had two individual spray booths which had been sufficient for their needs in the past but, they weren’t in the ideal location, and both booths were now nearing the end of their serviceable life. Paul Dudley continues: “We have a long history with Dust Control Systems; they’ve maintained our extraction system for many years, and have previously installed an Ecogate extraction optimisation system for us, and a highly-efficient 110,000 m3/hr Schuko filter. We have always been delighted with their product quality, their engineering know-how and, in particular, their attitude to customer service. When we knew the time had come to invest in a new spray booth, we had no hesitation in calling in Gallito (one of the DCS group of companies) to present a design proposal.”
Following a site visit to Ellis Furniture, Ian Ward, former Managing Director of Gallito Ltd, put forward a proposal for a fully contained 50m2 enclosure, housing three separate 3000mm wide dry filter spray booths; providing a working floor area of almost 40m2, a working height of 2960mm, and a total filter area of over 20 sq. metres. The enclosure is manufactured from 1.2mm thick galvanised folded panels, bolted together and sealed, and product entry and exit is provided by centrally located, self-closing double hinged doors. A separate personnel access door is located at one end, and double doors at the opposite end allow access to an existing drying room.
Clean filtered air is drawn from the factory by fans located above the enclosure, and lighting is provided by twelve 1500mm long twin fluorescent fittings. Each booth is served by its own 710mm diameter 3kW axial fan, running at 1400rpm and extracting up to 3.37m3 per second. 710mm diameter ducting, routed between roof trusses and out through the roof, allows vertical discharge of filtered air to atmosphere. Inside the enclosure, the spraying area comprises three standard Gallito DFB300 plenums fitted side by side – two 1000mm deep removable partitions allow each 3 metre wide area to be used independently or, when the partitions are removed, provide a working width up to 9 metres.
Ian Ward, commenting on the Ellis installation, said: “To ensure a long, trouble-free working life, Gallito booths are built to the highest standards, using premium grade materials, and all galvanised panels are cut to size on a CNC laser cutter, then folded and formed to give a perfect fit and seal.” “Gallito’s engineers completed the installation and commissioned our new spray facility in a one week window we had earmarked for the work”, says Paul Dudley, “and we are delighted with the quality of the whole structure. The installation now allows us to produce short runs economically, to a quality controlled standard, and we also use the booths to produce accurate sample products for client approval prior to volume production on the automatic spray line.”
For more information: Tel: 01952 290500 or email sales@filtermist.com.